Why is it important to study or work with equipment equipped with quality SCADA software?
In today’s rapidly advancing world, where technology is making giant strides, the quality and integrity of software have become essential factors for success across various domains, ranging from education and research to the industrial sector. Particularly when it comes to software employed in areas like industrial process management and automation, as exemplified by Supervisory Control and Data Acquisition (SCADA) systems, their significance cannot be overstated.
Top-notch software entails not only efficient and seamless operation but also the capacity to address all the needs and challenges posed by a specific task. In the realms of education and research, the comprehensiveness of the software can profoundly influence the depth and breadth of knowledge acquired. In the industrial landscape, comprehensive software translates into more effective process management, heightened productivity, and ultimately sustainable business expansion.
Top-notch software entails not only efficient and seamless operation but also the capacity to address all the needs and challenges posed by a specific task. In the realms of education and research, the comprehensiveness of the software can profoundly influence the depth and breadth of knowledge acquired. In the industrial landscape, comprehensive software translates into more effective process management, heightened productivity, and ultimately sustainable business expansion.
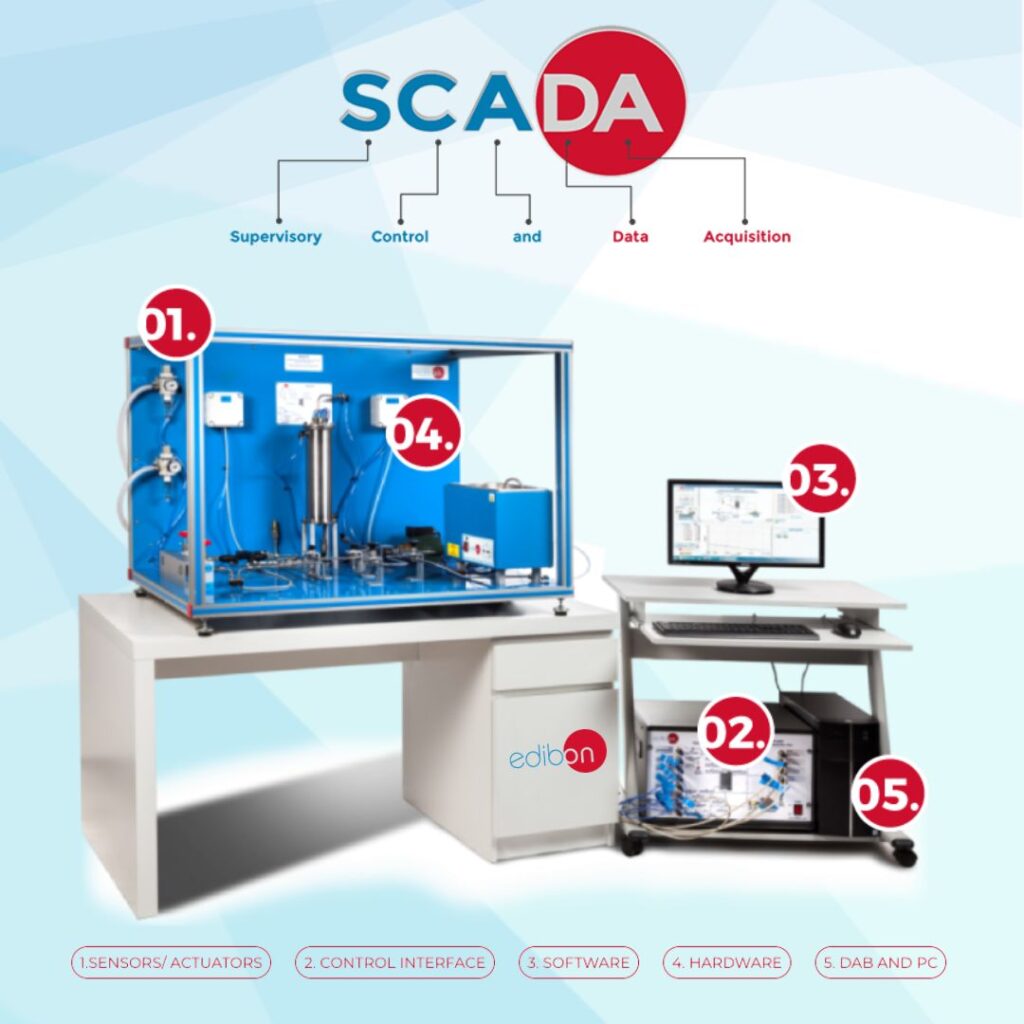
What do you receive when obtaining an EDIBON software for one of our equipment?
The following software is part of our SCADA application and is included in all computer-controlled EDIBON equipment.
Therefore, when you receive an EDIBON software, this is everything you receive:
1. Supervisory Software:
This software actively monitors parameters and process elements in real-time. When necessary, it takes action to prevent physical damage to the unit and users.
It comprises the following software components:
Alarm and Event Software Package:
- Warnings for extreme operating conditions: This software package notifies the user when process variables exceed or fall below normal levels.
- Operating limits: This package includes functions that supervise whether the process’s operational range is correct, ensuring safety for both users and the unit.
- Recommendations and cautions: This software package provides guidance on working with the unit, warning against actions that might lead to improper operation.
Process and Variable Monitoring Software Package:
- System process status: This package continuously monitors the process status. If necessary, it halts processes to prevent unit and user damage.
- System start and stop: This package initializes processes before transitioning to normal operation and safely stops the system.
- Real-time variable processing: This software processes sensor data to obtain accurate values for controlled system variables.
Response for Incorrect and Unexpected Conditions Software Package:
- System faults: This software package offers a User Interface for simulating hardware faults. Instructors can select from a range of faults to apply to the Data Acquisition System and Control System.
- Prevention of improper operating conditions: This package prevents users from working with the process and unit improperly by disabling system element actuation.
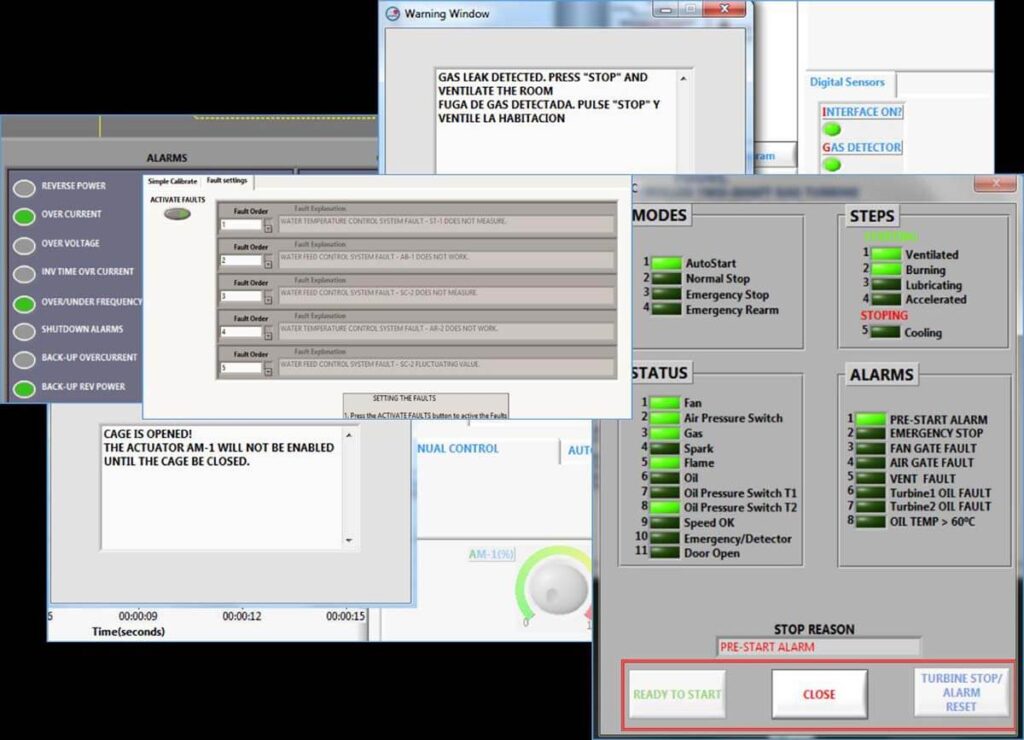
2. Control Software:
This software manages the system in either manual or automatic mode using appropriate control methods for the specific process.
It comprises the following software packages:
Real-Time Control Software Package:
- Closed-loop PLC control: This software establishes PLC communication to control system variables. Users can adjust PLC parameters to modify system behavior.
- Deterministic control loops: This package maintains execution speed to ensure accurate variable readings and real-time system element actuation.
Multi-Control Software Package:
- Multivariable control: This software manages multiple system variables for specific processes or simultaneous control of several processes.
- Multiloop control: This package synchronizes multiple loops, sharing readouts and statuses from system variables, controlling instructions during system operation.
Advanced Closed Control Software Package:
- Closed-loop PID control: This software implements Proportional, Integral, and Derivative Control, with adjustable PID parameters and factory settings restoration.
- Closed-loop PWM control: This package performs Pulse Width Modulation Control, adjusting the controller output’s duty cycle.
- Closed-loop time proportional control: This software controls the controller output’s time on system elements to reach a fixed setpoint, with user-accessible parameters.
Basic Closed Control Software Package:
- Closed ON-OFF control: This software executes a practical method for controlling less complex processes.
- Closed hysteresis control: This package utilizes a control method that introduces significant changes in the controller output whenever variables cross the hysteresis band boundaries.